Decaser for Round & Oval Containers
Model 49
Automate your reshipper uncasing with this compact system that unloads and single files, and handles empty cases, all in continuous operation. You’ll eliminate the tiresome task of unloading cases, improve plant safety, and ensure a consistent container supply to your line.
Robust and Reliable Solution for Reshipper Uncasing
Offering a solid combination of speed, flexibility, and gentle container handling, this decaser has earned its reputation as a preferred solution for food and beverage manufacturers who buy containers in reshipper cases.
- Uncase glass or plastic bottles from RSC, HSC, and RSC-Tablock style cases
- Eliminate manual labor and liability, and reduce production costs
- Maintain a consistent container supply to the filler
- Gentle handling for optimum container integrity and stability
Case size variations are easily accommodated on the Model 49 decaser. The case transfer system combines an automatic tensioner with soft compression rollers that accept varying case dimensions, ensuring smooth and gentle case transfer. The 180-degree case turnover has finger-style grippers that bend to securely hold even cases that are slightly off-spec during transfer to the overhead discharge conveyor.
Key Features That Benefit Your Production
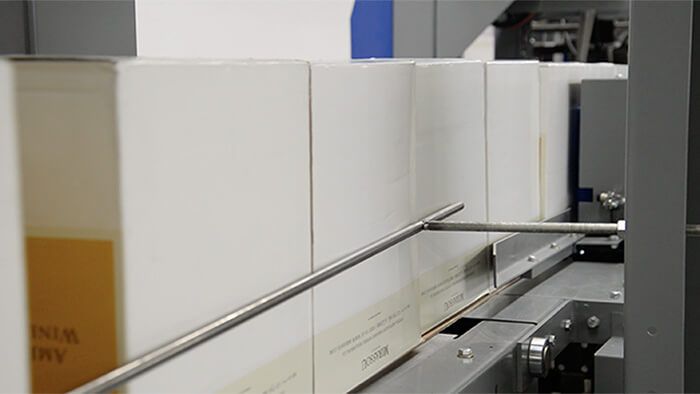
All-in-one system provides high speed, in-line operation
Cases may feed directly from the case depalletizer to the decaser. They are automatically timed from back-to-back or random spacing to the vertical belt infeed. An optional 180 degree inverter is available to feed cases from overhead conveyor.
The belt infeed provides gentle case handling and positively transfers cases to unloading. It is designed with an automatic tensioner and backed by soft compression rollers to feed all cases regardless of inherent case size variations.
Major flaps are plowed open and the minor flaps are opened by the container weight as the case is lifted. The containers discharge onto the impact absorbing transfer belt and are quickly single-filed for transfer directly to the production line.
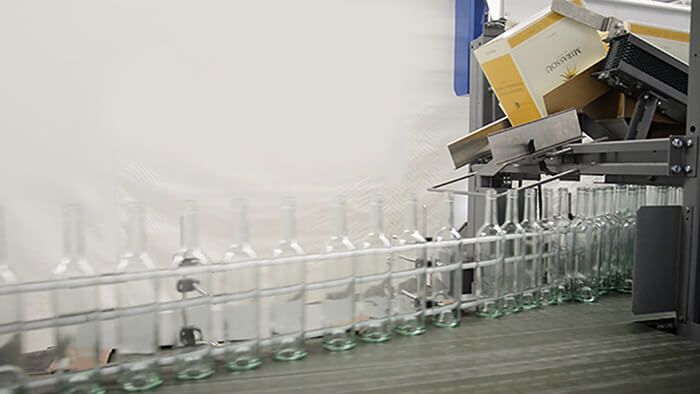
Improve line reliability and enhance employee safety while reducing costs
The Model 49 automates the repetitive and tiresome task of manual decasing, relieving the challenges of maintaining a manual crew, and eliminating the risk of employee injury or disability. It is a complete solution, from case feed through unloading and single filing that provides a non-stop container supply to your line.
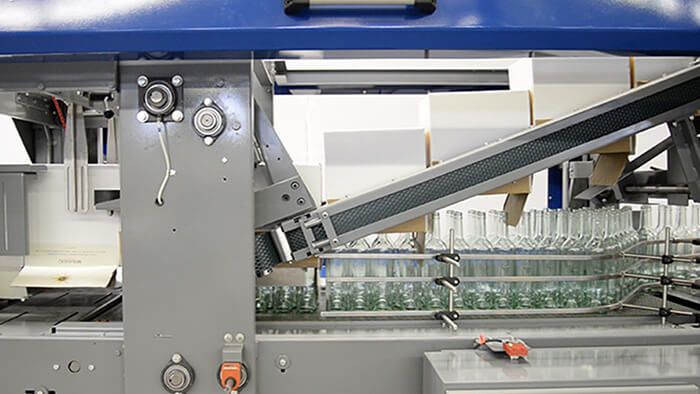
Gain top container integrity and stability with minimum contact
Bottles and containers glide from the case to an impact-absorbing belt and remain in their pack pattern, spaced and separate, until single filed with minimum contact.
This technique is production-proven to maintain glass container integrity and keep plastic containers upright and stable throughout unloading and single filing.
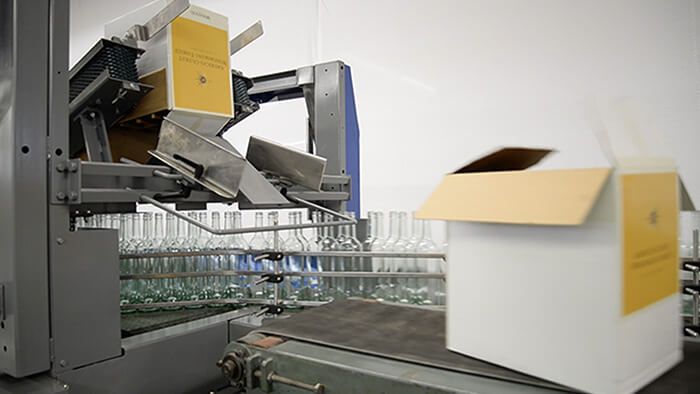
Cases are automatically uprighted for transfer to case packing
Empty cases are uprighted automatically for transfer to the case packer. An optional 180 degree case turner orients cases for overhead transfer.
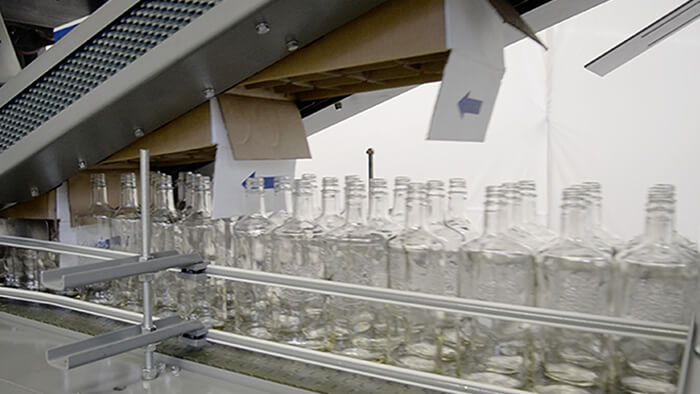
A versatile solution for current and future requirements
The Model 49 automatically decases and single files glass or plastic bottles from RSC, HSC, or Tablock cases. Changeover is quick and easy with most case changes completed with simple hand crank adjustments.
Specifications, Standard Features and Options
Speed: Up to 70 cases/minute
Case range: RSC cases, RSC-Tablock cases
(Tablock cases require 180 degree full case inverter)
Standard Features:
- Solid channel steel frame construction
- Allen-Bradley PLC
- Automatic case infeed- cases feed spaced or back-to-back
- Motor-driven dual vertical side belt case drive
- Impact-absorbing rubber bottle discharge belt
Independent single filing chains that minimize bottle-to-bottle contact - Automatic case turnover uprights cases to customer’s powered conveyor
- Non-contact sensors monitor machine operation
- Sealed bearings throughout
- High visibility guards with safety interlock
- Quick-adjust turn handles for case changeover
- Locking side bar adjustments
- High visibility guards with non-contact safety interlocks
- Grace Port PLC access
Options:
- CAT 3 Safety Circuits PL(d) or PL(e)
- Multicolor machine status lighting
- 180 degree full case inverter- to receive cases from overhead conveyor
- Outer flap pre-breaker- relieves flap memory to facilitate case packing
- 180 degree empty case turnover- uprights cases with four flap control
- Repeatable position indicators for changeover
- Locking guard door switches
How Can We Help?
Do you need help finding the best decaser for your packaging line?
Our packaging machine specialists are here to assist you in specifying the best uncasing solutions for your requirements. Call us and we will be happy to discuss your product and applications.